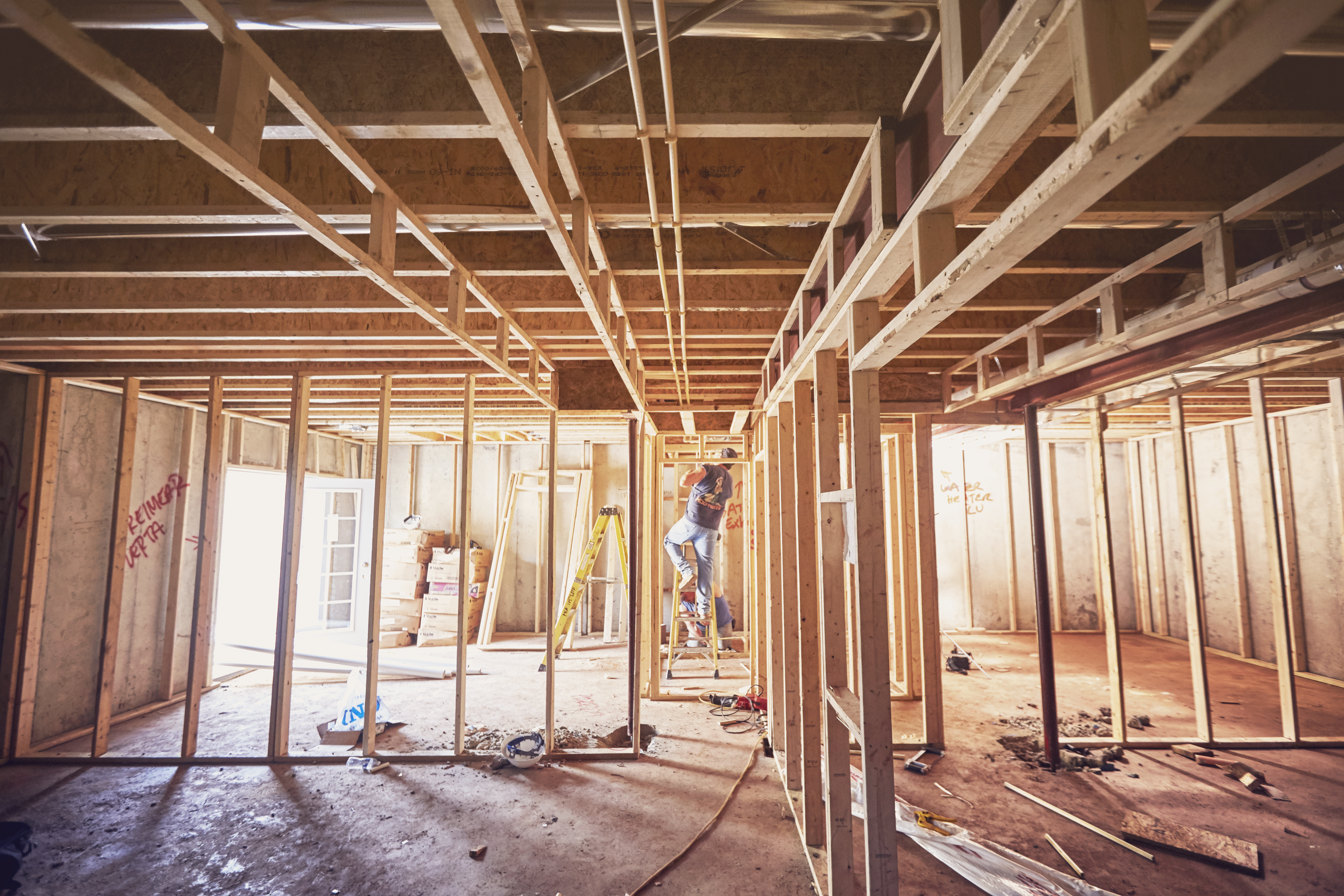
By: Jonathan Simon on September 21st, 2021
Best Practices for Plumbing Multi-Family Projects
Multi-Family | pvc | CPVC
While there are many differences between single-family and multi-family construction, when it comes to plumbing, they have more in common than not. But the size of these buildings can amplify the cost and consequences of poor material choices and design decisions. The cost of poor decision—whether in the design or during installation—isn’t limited to just one home. It can be multiplied across every unit in the complex.
Here are some of the considerations that require extra attention when planning plumbing for a multi-family home.
Ensuring Material Compatibility with Water Conditions
Any plumbing leak can be expensive and inconvenient, but when that leak occurs in a multi-family building, the damage may not be contained to a single unit and the cost of repairs can skyrocket. Engineers and owners should work with plumbing contractors to ensure plumbing materials are compatible with local water conditions.
There are multiple real-world factors that make PEX piping vulnerable to chlorine degradation and one of those factors is the oxidative reduction potential (ORP) of the water flowing through the pipes. The ORP in municipal water systems is intentionally driven up by the chlorine-based disinfectants used in water treatment.
Chlorine-induced PEX failures can be accelerated by commercial hot water or pressures above 80psi – both conditions can be easily found in multi-family projects. Elevated pressures are especially common in buildings using booster pumps or gravity feed systems.
When PEX piping is exposed to these conditions, it can suffer chlorine degradation and premature failure, as outlined in the Plastic Pipe Institute’s Technical Note 53.
Copper can suffer similar effects from chlorine, but there is one material that does not suffer from chlorine compatibility issues: CPVC. As a chlorinated compound, FlowGuard Gold® CPVC is immune to degradation from drinking water treated with chlorine-based disinfectants and is an ideal choice for multi-family projects, regardless of local water conditions.
Material Cost Management
The bigger the job, the more you can save by ensuring contractors make smart material choices. The difference in material costs between FlowGuard Gold CPVC and PEX is not insignificant. In fact, one of the leading manufacturers of PEX published a cost study for a four-story, 91-unit hotel that showed CPVC delivered more than $10,000 in savings over PEX.
If a hot water recirculating system is planned for the building, PEX’s vulnerability to chlorine may further increase costs. A PEX hot water circulation system may be limited to two feet per second water velocity by code and manufacturer recommendations. Maintaining adequate water volume at those low velocities can require significant upsizing, further increasing the cost differential between PEX and CPVC.
If you expect to make up that difference with faster installation, you’ll probably be disappointed. Home Innovation Research Labs conducted a time study of the most common installations of FlowGuard Gold CPVC and PEX and found that, in trunk-and-branch systems, CPVC installed 15% faster than PEX. PEX manifold systems installed 11% faster than a CPVC trunk-and-branch system, but the manifold used 21% more pipe, offsetting the savings in installation time.
Improving Energy and Water Efficiency
As evidenced by the Home Innovation study, manifold systems can reduce installation times, and when properly configured, can improve water and energy efficiency.
Until recently, contractors that wanted to use the manifold system were limited to PEX as CPVC manifolds weren’t available. But with the introduction of the 1” x ½” 3-port FlowGuard MultiPorts, plumbers no longer have to compromise reliability and performance to use a manifold system.
The introduction of CPVC manifolds could also help prevent a common design error in the application of manifolds. The efficiency benefits of manifolds are only realized when branch lines are kept short. Yet, the flexibility of PEX piping encourages plumbers to pay less attention to the location of the manifold and run long branches. This not only neutralizes the efficiency benefits of the manifold but is another factor that drives up PEX material costs. With the FlowGuard MultiPort, branch lines are kept short, and the efficiency of the system can be maximized.
Minimizing Pressure Drop
One of the misconceptions about PEX is that, because it uses fewer fittings than CPVC and copper, the pressure drop is minimized.
That might be the case if PEX used the same type of fitting as CPVC and copper, but it doesn’t. In copper and CPVC, the pipe is inserted into the fitting, maintaining full flow through the pipe. With PEX, the fitting is inserted into the pipe, reducing the diameter of the pipe at each fitting, and causing pressure drop that far exceed those that occur with copper or CPVC fittings. PEX expansion fittings, for example, which are sometimes marketed as “full flow” fittings, can reduce the pressure in the water system by as much as four (4) psi per fitting. With more fittings being used in larger buildings, the impact of PEX fitting on pressure at fixtures is magnified.
The Right Material for Multi-Family Homes
You’re probably already using CPVC for the mains and risers in a multi-family building. By ensuring that FlowGuard Gold CPVC is run through the units to the fixtures, rather than transitioning to PEX, allows the reliability, performance, and cost benefits of CPVC to be extended throughout the building.
The benefits of FlowGuard Gold CPVC over PEX are amplified in multi-family homes. Ensuring FlowGuard Gold pipes and fittings are used in your project can reduce risk, lower costs and improve plumbing system performance. Download our brochure to learn more about the benefits of FlowGuard Gold CPVC and how easy it is to Make the Switch.