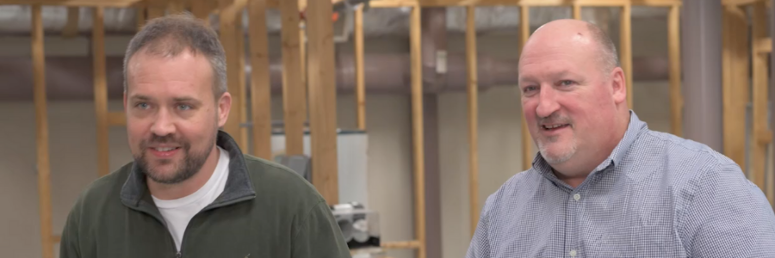
By: Jonathan Simon on April 30th, 2020
Plumbing Express Shares Insights on Re-Piping and Getting Five-Star Customer Reviews
PEX | re-pipe | Service Plumbers
Plumbing Express is a premier provider of re-piping and other plumbing services in the Atlanta metropolitan area. The company relies on FlowGuard Gold® pipe and fittings and consistently receives high customer ratings across a range of online sites. We spoke with general manager Ty Gailey and director of operations Blake Mowe to get their insights on building and maintaining a successful re-pipe service.
Q. Can you tell us a little about Plumbing Express?
Ty: We’re a full-service plumbing company with a specialty in re-piping. We have a turnkey re-pipe service that integrates plumbing and drywall repair, allowing us to deliver fast, coordinated re-piping services. When we finish a re-pipe our goal is that the homeowner can’t tell we’ve been there—except any plumbing problems they’ve been experiencing will be resolved.
Blake: We got our start re-piping with the lawsuit that ended the production of polybutylene in 1995. It created a fund for homeowners to replace failing polybutylene pipes and we won the bid for the Atlanta area. Atlanta was in the middle of a huge building boom for the 1996 Olympics at the time and a lot of polybutylene was being installed. We were doing 12-15 homes a week and we really perfected our approach to re-piping. We’ve been building on that experience ever since.
Q. How have you been able to receive consistently high ratings from customers?
Ty: We’ve been able to build and maintain an excellent reputation by exceeding homeowner expectations. We have experienced and trained plumbers, we arrive on time, respect the homeowner’s property, have an excellent 10-year warranty and use reliable, proven materials. FlowGuard Gold CPVC is the only material we use.
Blake: Our turnkey approach to re-piping is also a factor. When we have to access piping through walls, we cut out a piece of sheetrock about the size of a picture frame and label each piece so our drywall team can come in the next day and replace all the pieces. We also computer match the color so it’s not evident where we cut. When our customers see the holes in the walls the first day, they get a little freaked out. But then when we finish all the drywall work the next day, they are shocked at how good it looks.
Q: Why is there still such a demand for re-piping in the area when polybutylene hasn’t been in production for 25 years?
Ty: We still see some polybutylene today, as well as copper piping, that is experiencing pinhole leaks due to the disinfectants in water treatment. But the majority of the re-pipes we do involve PEX failures.
Blake: A lot of builders still use PEX, even on higher-priced homes, because they see it as a cheap and easy-to-install material. But it’s not a great long-term solution. We see problems with PEX in homes that are less than 20 years old. The material itself and the joining method both contribute to the problems we see. In fact, when we were doing projects under the polybutylene settlement, we weren’t allowed to use PEX because the crimp ring fittings installation method is identical to polybutylene. We had to use a welded system, so we turned to FlowGuard Gold CVPC. We’ve had a lot of success with that system.
Q: How do you convince homeowners a re-pipe is necessary in homes that are still relatively new?
Blake: Homeowners expect their plumbing to last a long time, so they are definitely frustrated when they realize their fairly new and not inexpensive home requires a re-pipe. But they also reach the point where the problems they are experiencing are so persistent they know they need to address the core of the problem. If that is substandard plumbing materials or improper installation, they don’t have much choice. Some are worried about losing their homeowner’s insurance because of the number of claims they’ve had to file. We present re-piping as an option when it is warranted. If they’ve been living with leaks for a while, it doesn’t take much convincing.
Q: Do you ever see problems with FlowGuard Gold CPVC?
Ty: In the few cases where we had to replace FlowGuard Gold CPVC, it was always due to either improper installation or damage to the pipe prior to the installation. As CPVC ages it gets harder and actually stronger from the inside out, but we do sometimes see issues when it was installed with too much stress on the joints and over time it causes an issue. It’s rare and it illustrates the importance of having trained plumbers do the installation. If you know what you’re doing, you won’t have any problems with CPVC.
Q: Why not use generic CPVC instead of FlowGuard Gold CPVC?
Blake: With FlowGuard Gold CPVC, we know exactly what we’re getting. Generic products may not be manufactured with the same high-performance expectations. If no one is willing to put their name on a product, you shouldn’t be putting it in somebody’s house.
Find out how you can give your customers the durability and performance of FlowGuard Gold pipes and fittings. Make the switch to FlowGuard Gold CPVC today.