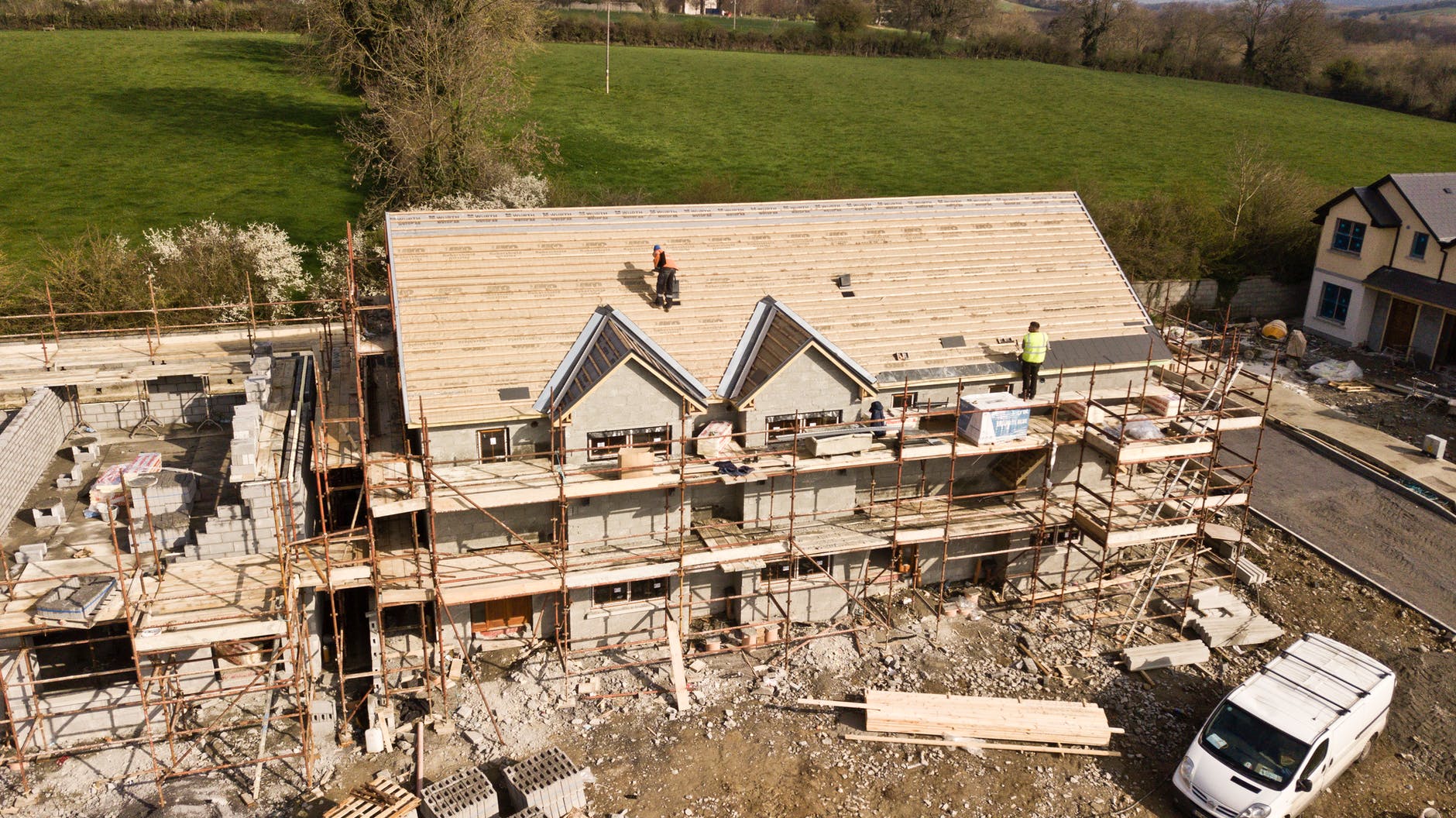
By: Jonathan Simon on November 20th, 2021
Quiz Reveals Builders’ Broad Knowledge of Risks and Limitations of Code, But Also Exposes Some Blind Spots
Following up on our successful Plumber’s Quiz, which exposed some critical misunderstandings around best practices for servicing plastic plumbing systems, the FlowGuard Gold team conducted a similar quiz for builders.
The quiz was completed by more than 300 builders and, for the most part, participants demonstrated good knowledge of the extent of their liability and the risks or relying too heavily on building codes to ensure performance and homeowner satisfaction. But there were notable areas of concern where many participants were unfamiliar with potential material defects or manufacturer practices that could leave them vulnerable.
The Blind Spots
More than half of participants thought the statement, “Some plumbing piping warranties can be voided by drinking water” was false, which is understandable yet a concerning blind spot amongst builders. One would assume that the warranty for a product designed to carry water wouldn’t be voided by that water. Yet, that is the case with PEX and Copper warranties as manufacturers just can’t guarantee their products won’t be affected by the chlorine-based chemicals in the water flowing through the pipe.
The other question that had a high percentage of incorrect answers asked participants what product category had the largest product defect settlement (class action suit) in U.S. history. Sixty-eight percent answered incorrectly, with 46% selecting drywall, 16% concrete and 6% flooring.
The correct answer was plumbing and pipe fittings, specifically the billion-dollar settlement reached over the widespread failure of polybutylene piping. There are two reasons this shouldn’t be that surprising. First, plumbing failures lead to water damage that is expensive to repair. Not only did more than 300,000 homes with polybutylene need to be re-piped, but the water-damaged drywall, flooring and cabinets also needed to be replaced.
The other reason is that plumbing defects can take years to reveal themselves through widespread failures. This is particularly true for materials that are sensitive to chlorine degradation. These materials have certain conditions which can accelerate degradation, one of which is the amount of disinfectants and other oxidizing agents in the water flowing through the pipe. Builders have no control over this variable and municipalities often adjust their water treatment practices to deal with changing conditions or growth of the distribution system. So, defects emerge years after the product was installed but much sooner than would be expected based on the anticipated product lifespan. In the case of polybutylene, by the time the defect was exposed, the material had been installed in hundreds of thousands of homes.
Where the Buck Stops
In general builders understand that, in many cases, the buck stops with them. This was apparent in one of the early quiz questions that asked whether a builder is responsible for the performance of code-compliant products selected by subcontractors. Over 90% understood they were responsible for product performance, even if products met code requirements.
Participants also understood the limitations of building codes in dealing with problem materials. Ninety-two percent correctly answered “false” to the question: “Federal, state and local building codes have taken all problem materials out of the market; thus, any product that is available is deemed to be safe regardless of where it is being used.” As we saw with polybutylene, it can take years for defects in a product to become widespread enough to be restricted by code, particularly in the case of plumbing materials that can’t hold up to local water conditions.
A lower percentage (62%) recognized that just because a home passes inspection doesn’t necessarily mean it was built properly. The drop-off in awareness of potential liability issues got even steeper regarding the extent of the protection provided by licensing regulations. Only 56% understood that state and local licensing requirements, while important, do not ensure homes are built correctly by qualified workers.
Complying with codes and using properly licensed subcontractors is essential, but mere compliance doesn’t ensure quality and long-term performance. Many states only require one company employee to hold a trade license, while the actual installing labor force may not be licensed or trained at all. This can lead contractors to argue that they need to use more “fool proof” products; however, every product in a home needs to be installed correctly and product selection cannot overcome an untrained labor force. If the wrong materials are selected for critical systems such as plumbing, the quality of the home is compromised.
Building Healthy Homes
Delivering healthy homes is becoming increasingly important and, while 100% of builders recognized indoor air quality as an important component of a healthy home, 30% missed the importance of water quality. Those outside the industry may see water quality as the sole province of the municipality, but many builders understand plumbing material selection has an impact on water quality.
PEX pipe has been shown to have a higher biofilm growth potential than other plumbing materials, increasing the risk of bacteria entering the water supply. PEX can be susceptible to permeation in addition to leaching above regulated levels for some states, both of which can impact water quality. Corrosion in copper piping can lead to levels of copper in the drinking water that exceed health guidelines and cause bitter or metallic tasting water that is off-putting to homeowners. While no material can improve water quality, CPVC pipes have a lower biofilm growth potential than PEX and are not susceptible to permeation or chlorine degradation, minimizing the impact of plumbing materials on water quality.
Protect Against Premature Failure
Builders may not be able to be involved in every decision made during the home building process, but one that does require their attention is plumbing material selection. The wrong materials can increase the builder’s risk exposure, regardless of whether the material meets code requirements and is installed properly.
FlowGuard Gold CPVC outperforms copper and PEX in resisting damage from water treatment chemicals municipalities add to the water supply. CPVC has been used for domestic water systems in the U.S. for more than 60 years and is engineered and manufactured to the highest standards. Give yourself one less thing to worry about by making the switch to FlowGuard Gold CPVC for your next project.